Cet article fait partie d’une série dont il est recommandé de commencer par la Partie 1
La Schématisation
J’ai commencé par réaliser un schéma électronique avec toutes les fonctionnalités nécessaires et leur raccordement aux entrées/sorties du microcontrôleur.
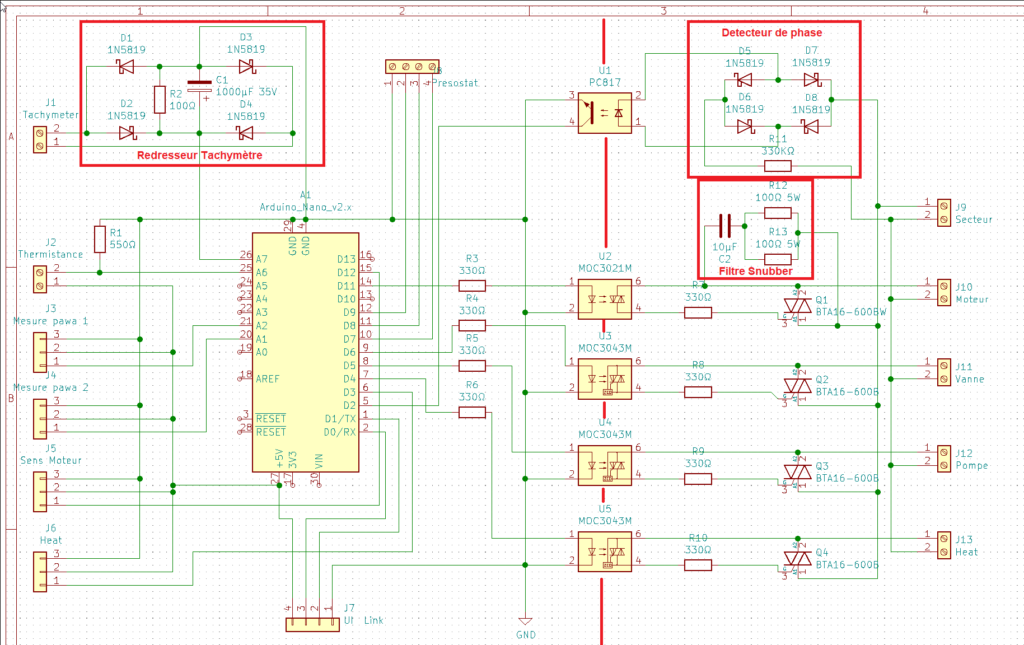
Le schéma est composé de 2 parties distinctes. La partie basse tension en 5VDC (à gauche) et la partie secteur en 230VAC (à droite) sont séparées par des optocoupleurs et optotriacs pour assurer une isolation galvanique.
Le microcontrôleur (un Arduino Nano) est connecté à différents sous-circuits :
En haut à gauche du schéma se trouve un circuit redresseur servant à convertir la tension alternative fournie par le tachymètre en une tension continue afin de permettre au microcontrôleur de mesurer la vitesse de rotation du tambour.
En haut à droite se trouve un autre circuit redresseur permettant de détecter la phase du secteur. Il s’agit d’un des éléments composant le gradateur à angle de phase utilisé pour contrôler la vitesse de rotation du moteur. Je détaille plus précisément son fonctionnement dans la partie 8.1(à venir).
En dessous, j’ai ajouté un filtre snubber (RC) ayant pour but d’absorber les pics de courant venant du moteur lors de la commutation. Le moteur état principalement inductif et étant très souvent commuté (à cause du gradateur), des pics de courant pourraient endommager le circuit et le moteur. Même si finalement, le fait d’utiliser un triac snuberless semble suffire à remplacer ce filtre.
Le Prototype
J’ai d’abord réalisé une première version de ce circuit afin de tester si le dimensionnement des différents composants était correcte.
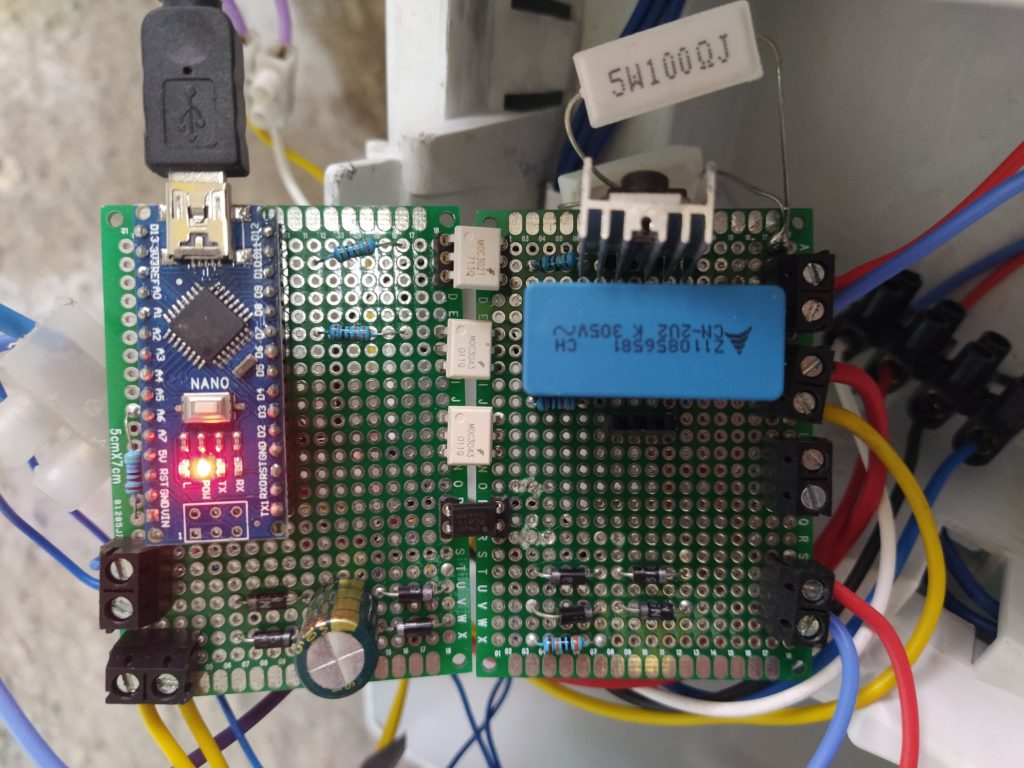
Les composants sont montés sur des supports pour pouvoir les remplacer facilement. J’avoue en avoir grillé quelques-uns lors de cette étape.
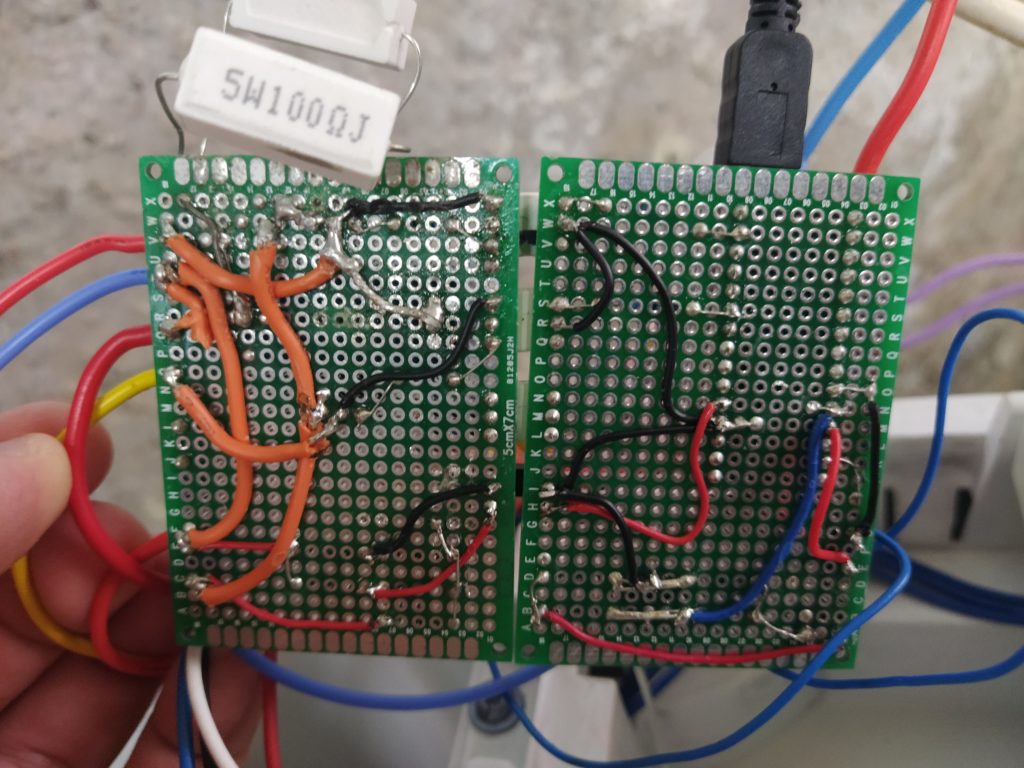
Même si la séparation entre basse et haute tension était plutôt bien respectée grâce à 2 PCB distincts. Je ne suis quand même pas serein de laisser un tel circuit « en production ».
La réalisation du PCB
Je pars du schéma électronique pour réaliser un routage. Le PCB sera simple face, mais j’utilise une seconde face pour représenter les jumpers.
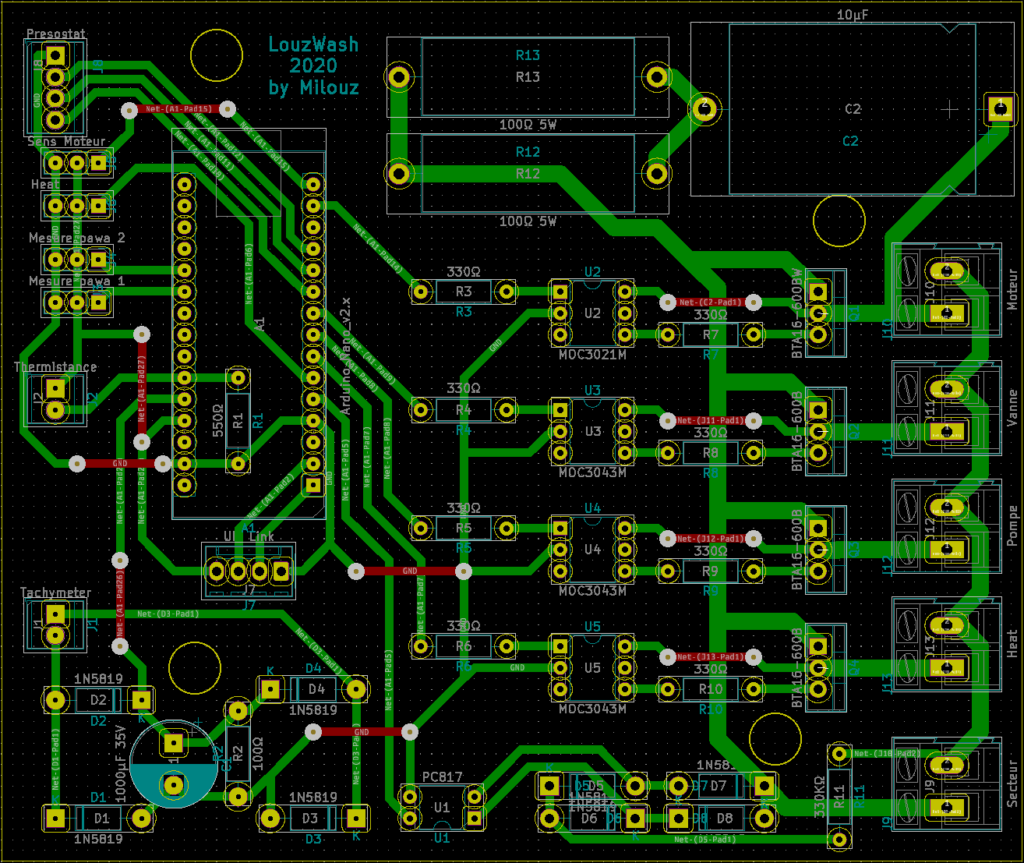
J’ai d’abord choisi l’option de réaliser mon propre PCB à l’aide (entre autre) d’une imprimante 3D. Je détaille cette étape dans la partie 8.2. Mais face aux problèmes rencontrés (no spoil) je décide de le faire réaliser.
Après avoir comparé avec PCBWay, je décide faire appel aux services de JLCPCB. Le résultat est top. Le seul hic avec ces plateformes est de devoir commander une quantité minimum de 5 exemplaires.
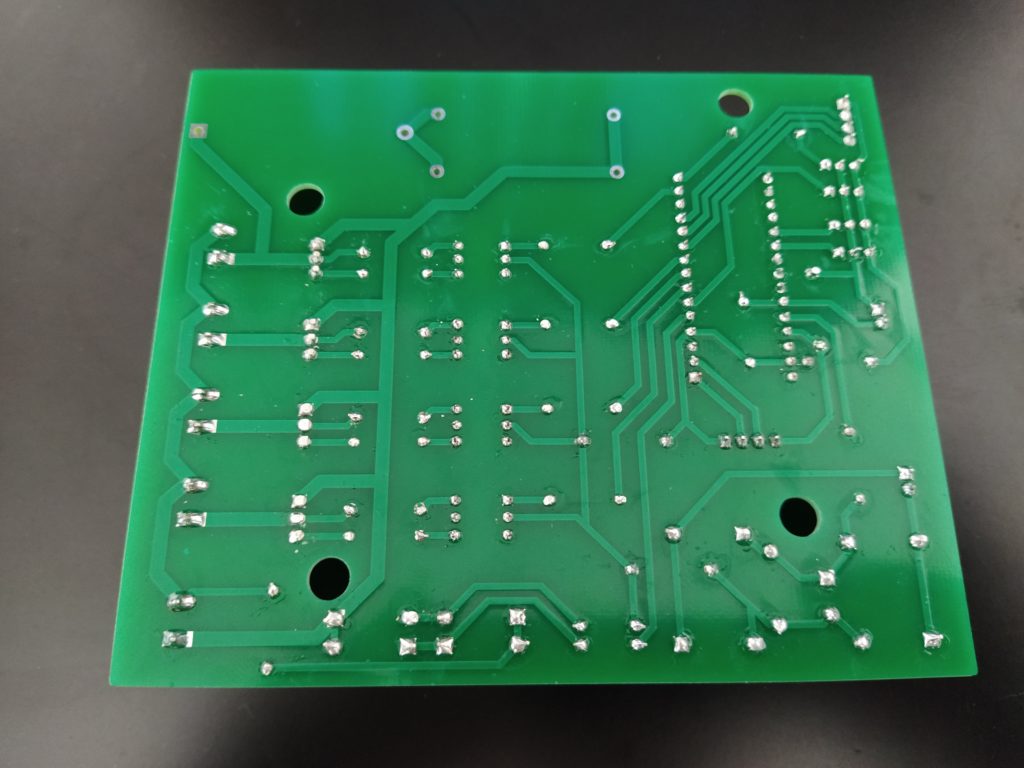
À part quelques erreurs de ma part : quelque trous trop petits que j’ai dû repercer et du masquage sur les via que j’ai dû gratter, je suis vraiment content du résultat.
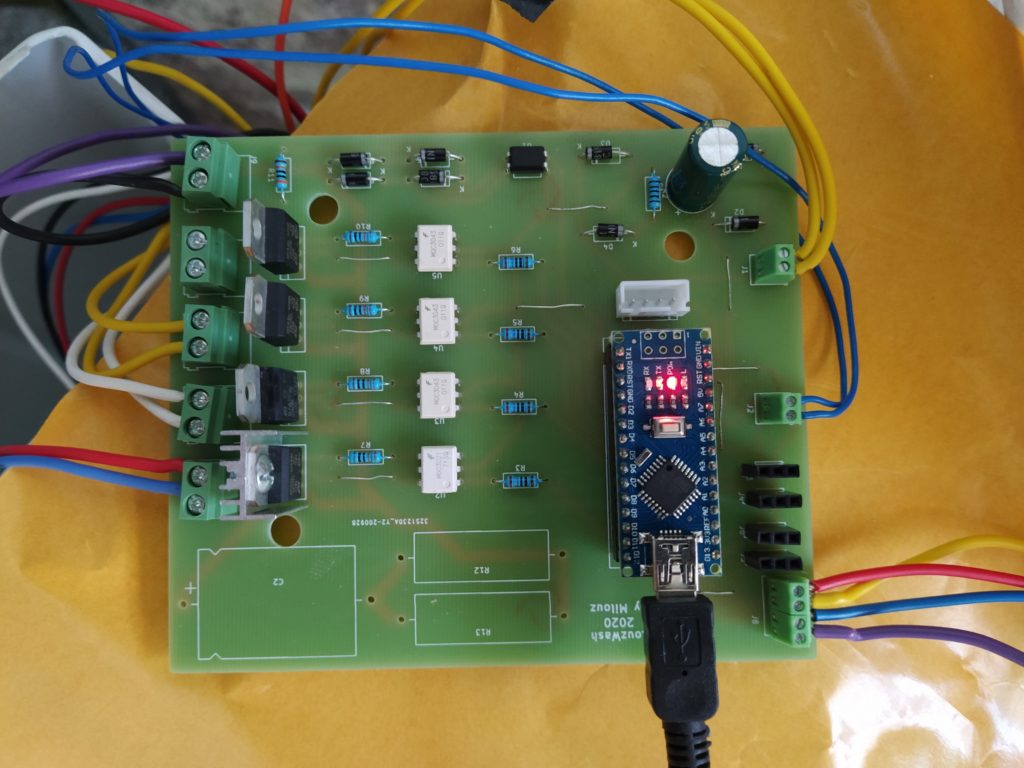
Il reste maintenant à assembler les différents éléments dans la partie 9.
Bonjour,
Je vous félicite pour ce chouette projet. Je me demande si la partie 8.1 est publiée quelque part, ou bien elle n’est pas encore publiée.
J’ai plusieurs questions par rapport au circuit kiCAD publié ci-dessus :
Quelle est la valeur ajoutée du circuit détecteur de phase (en haut à droite) et en quoi il vas être utile. ?
Puis est ce que les tachymètres utilisés dans les machines à laver on la même tension de sortie ?
A quoi il sert le connecteur J6 puisque vous utilisez déjà le connecteur J2 pour mesurer la température de l’eau ?
Est ce que la mesure de courant se fait via des capteurs de courants fournie avec le lave linge, ou bien c’est vous qui les a ajoutés ?
Et ma dernière question, pourquoi vous utilisé des opto-triac à détection de zéro pour les tout les actionneurs sauf le moteur ?
Je m’excuse les nombreuse questions, mais je suis vraiment intéressé par ce projet.
Dans l’attente de votre retour.
Cordialement.
C’est clair que ce projet mérite plus de mise en avant. Ce que vous faites, c’est en gros un lave-linge Open-Source si je comprends bien? Il mériterait une page sur Github/Gitlab avec une traduction en anglais.
Evidemment, à la base vous reprenez un lave-linge existant. Mais je ne pense pas qu’il y ait beaucoup d’autres choix. Mais je pense que l’on pourrait facilement l’adapter à d’autres modèles ou changer toutes l’électronique (moteurs, capteurs et autres) pour ne pas être dépendant des spécifications d’un constructeur. Seul le tambour ou est le linge est impossible à se procurer facilement.